ClearPower Modules Tackle Designers’ Toughest Challenges
There are fundamental truths that every system designer must face when it comes to power electronics. First, most projects will need multiple rounds of design, simulation, and trial to pass strict limits on EMI (electromagnetic interference). Second, there is the issue that introducing EMI components will reduce system efficiency and add to cost and solution size. This latter point is particularly pertinent as there is often very little board space reserved for the power solution, so the option of using large, proven solutions is no longer valid. Finally, the thermal environment will generally be worse than anticipated.
Fortunately, where this situation was once little short of dire, recent developments in integrated circuit design, system integration and packaging are serving to lighten the power designer’s load. In fact, it is now possible to consistently deliver high-quality designs that pass the strict limits of CISPR 25 Class 5 or EN 55025, while simultaneously reducing overall solution size and managing thermal dissipation.
Allegro MicroSystems’ ClearPower module family of products, which adopt a ‘system in a package’ approach, provide the answer that designers have been seeking for some time. ClearPower modules house all the principal elements of a high-performance switching power supply or LED driver within a compact package, significantly easing the task of designing complete power solutions.
An example of a recently developed ClearPower module is Allegro’s APM80900 (Figure 1), which is intended for LED lighting applications. A power inductor, critical bypass capacitors and an advanced switching regulator IC are co-packaged within an envelope that measures just 4 × 6 × 2 mm, while routable substrate technology is employed to connect the various sub-components together, and to the outside world.
By co-locating these critical power stage components within close confines, the high current switching paths that promote EMI are reduced by a factor of 10. Additionally, through direct integration and innovative IC design, overall size can be up to 70% less compared with conventional solutions.
Allegro MicroSystems’ ClearPower modules feature an MIS (molded interconnect substrate) routable lead-frame package with the look and feel of a conventional QFN solution. Combining this technology in an industry standard QFN footprint with wettable flanks ensures reliable operation at the harshest of automotive operating temperatures.
While the task of developing a viable power solution that will pass EMI limits has become far easier with power modules, achieving high performance demands a holistic approach to the design of the module itself. This undertaking involves combining IC design, packaging technology and passive component integration to achieve the desired EMI, thermal performance and size.

Specialized packaging and chip design techniques allow ClearPower modules to achieve excellent thermal dissipation characteristics. This factor is critical as both the IC and inductor are heat sources and are encased within the same compact package. Notably, deploying multilayer routable packaging technology within the ClearPower module, which is not possible with conventional single-layer lead-frames, permits the creation of connections and component spacing that maximizes thermal dissipation. The routable inner layer(s) of the module package is used to make contact with the IC and passive components, while the module’s heat-generating areas (power switches and inductor) are connected through vias, providing an efficient way to channel heat from the package interior to its large, exposed power pads.
Flip-chip IC technology is often used to lower the resistance and inductance associated with bond wires. Just one flip-chip connection (referred to as a bump) has an inductance around 20 times less than a conventional bond wire. As a result, multiple bumps can be used to connect to each high-power node, producing a total inductance that is immeasurably small. Flip-chip bumps also lower any high-frequency ringing that leads to EMI and, in comparison with conventionally bonded products, serve to decrease power dissipation.
In addition to these advanced packaging techniques, ClearPower module-based regulators (including the AMP80900) use many of the same techniques as conventional switching regulators to further reduce EMI. One method is spread spectrum modulation, which slightly modulates the converter's switching frequency. Here, energy is spread out over a broader frequency span to reduce noise energy peaks. Another effective method of reducing EMI is by reducing switch turn-on losses. ClearPower modules are uniquely designed and configured to minimize such losses.
Once a power supply design has gone through its initial stages, EMI is evaluated in a special testing laboratory, often leading to late nights, stressed engineering managers and inconvenient late-stage design modifications. As EMI laboratory time is typically charged by the hour, it is incumbent upon the design team to reach a viable EMI solution quickly. This demand leads to any number of non-ideal solutions being employed to quell EMI, including metal shields, passive snubbers and common mode input chokes. These additional passives add cost, increase overall size and reduce system efficiency, leading to higher heat dissipation.
The promise of ClearPower modules is that there is no longer any need for these somewhat desperate measures. Today, a CISPR 25 Class 5 compliant solution can be delivered with far less effort. To prove this point, a like-for-like comparison between a module solution and conventional counterpart is shown in Figure 2. Both designs employ identical input filters and switch at 2.5 MHz. Note that the module design is typically very close to the noise floor of the measurement system and exhibits considerably less noise than the conventional design.

Alongside EMI concerns, reducing the power solution envelope and profile on the board is an ongoing challenge. While every type of electronic component requires a power supply to perform its function, this notion often occurs late in the process and receives little attention. Treating the power supply as an afterthought means an optimum design will not be achieved, promoting many system problems. Allegro’s ClearPower modules are viable solutions that improve performance and simplify design. Moreover, by reducing external components, integrating magnetics and using bespoke power packaging designed to withstand the harshest automotive operating temperature range, ClearPower modules can reduce overall solution size by up to 70%, as outlined in Figure 3.
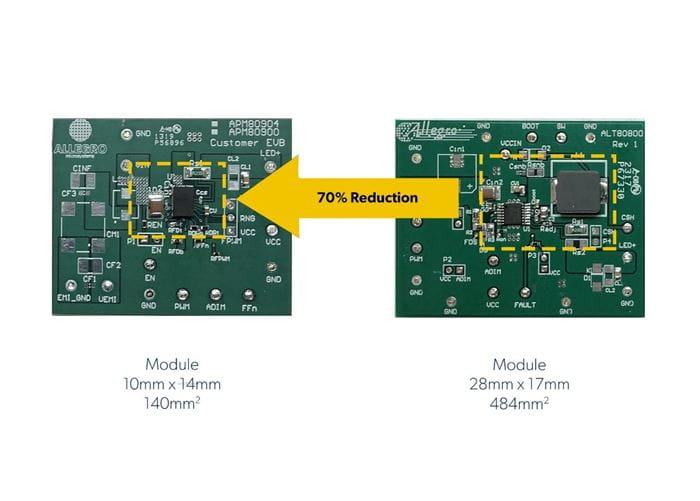
Ultimately, EMI mitigation is an increasing challenge as more systems become connected wirelessly or are integrated into smaller spaces where there is a higher potential to interfere with other devices. ClearPower modules from Allegro MicroSystems offer a fast, effective and reliable solution for solving these difficult EMI challenges. In addition, ClearPower modules reduce R&D time and cost, and simplify the bill of materials, while the PCB area required for the power solution is significantly reduced, leaving space for more value-added functions. In short, power modules are becoming increasingly mainstream and compare favorably in the overall cost-benefit calculations of system developers.
Originally published in Bodo’s Power Systems’ Magazine PCIM Europe Show Edition for July 2020. Republished with permission. Download Original PDF